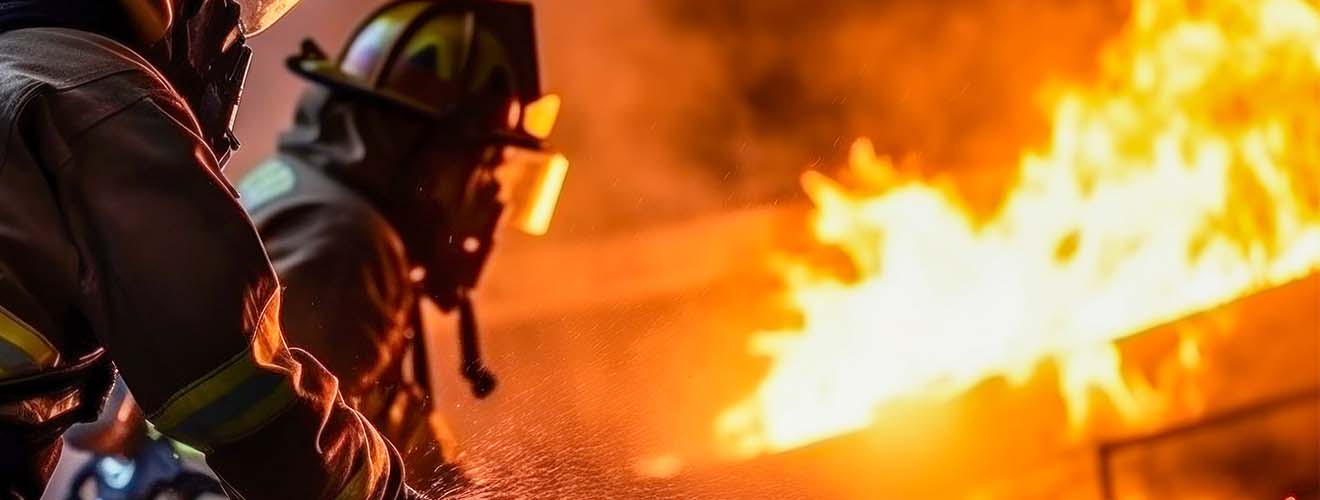
Customer Requirements
In this case, customer’s communication cable must be reliable under extreme condition, in a firefighting environment, therefore customer requested advance telecommunicated cable that can operate flawlessly under extreme temperature environment. In order to accomplish this ultimate goal, the design require highly dependable material, innovated product structure, advance product assembly, along with first-rate functional testing, due to every aspect of the function of this cable could be severe factor in firefighters working environment and its performance need.
Challenge Review
● Required to pass all mechanical testing after thermal shock with basic conditions of fireproof material, high temperature resistance and air tightness.
● Complies with ISO17493 and NFPA 1802 standard.
Supreme Charger Solutions
【Material Selection】
● Cable: Customer provided designated functional connection of communication signal and related reliability test requirement. In order to meet all reliability test requirement under high temperature condition, it required numerous experiment for different kind of material with different kind of compound ratio. We recorded all the data of reliability testing for each solution in order to find out best formula that provide most suitable overall performance.
● Plastic components: Beside the basic condition of fireproof and heat resistance, we needed to create a stable environment for electronic component to be installed was another important factor that our design needed to overcome with. Eventually, we had selected a unique plastic material that can withstand near 300°C and could be used flawlessly under high temperature environment without melting.
● Sealing adhesive: Liquid is another very important factor that need to be considered under firefighting environment beside fireproof and heat resistance. Therefore, we used distinctive grade of sealing adhesive at all critical position to ensure air tightness of product.
【Structure】
The usual connector molding solution is not suitable for high temperature environment. More specifically, it is required to redesign molding structure to resolve additional force added to solder joint which caused by usual structure that would deform under high temperature and reduced tension.
【Reliability Test】
1.Mechanical testing:
More than 10 object need to be tested.
Bending Life Cycle Test (±90°, 180°)
Swing Test
Pull Test Certification
Anti-Rotation Test
Twist then Pull Test
Coil Extension / Retraction Test (Extended 300% Length)
Coil 5.5X Cyclic Extension Test
Maximium Coil Extension at Low and high Temperature Test
Cable Jacket Sandpaper Abrasion Test
Salt Spray Test
Insertion and Removal Force Test
Packaging – Vertical Random Vibration Test
2.Production testing:
6 air leak and functionality testing items.
Connectivity Test
Insulation Resistance Test
Hi-Pot Test
Fluke Cable/Network Test
Mechanical Vacuum Test / Leak Test
Function Test
3.High temperature resistance testing:
2 test items meet with international regulation beside thermal shock.
Thermal Shock Test
177°C 6 Cycles Heat and Immersion Leakage Test (Per NFPA 1802)
High Temperature 260°C 5 mins Test (Per ISO-17493)
【Testing Method】
1.In order to meet with customer’s high temperature test requirement especially for specific test that required completing by designated time, we had in house designed fixtures that could be able to withstand high temperature and easy to install/uninstall within limited time.
2.Functional testing: We had in-house designed testing equipment for designated signal in-put / out-put based on product’s functionality as there was no suitable equipment on the market that can meet customer’s testing requirement. Furthermore, our testing machine not only can meet with customer’s request to conduct real time functional test under high temperature but also record automatically for more precise outcome.

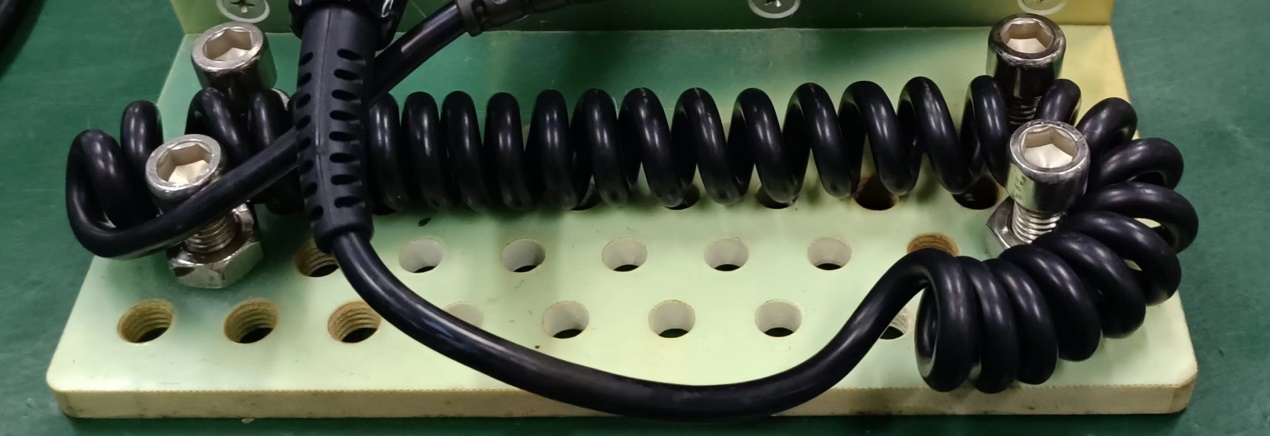